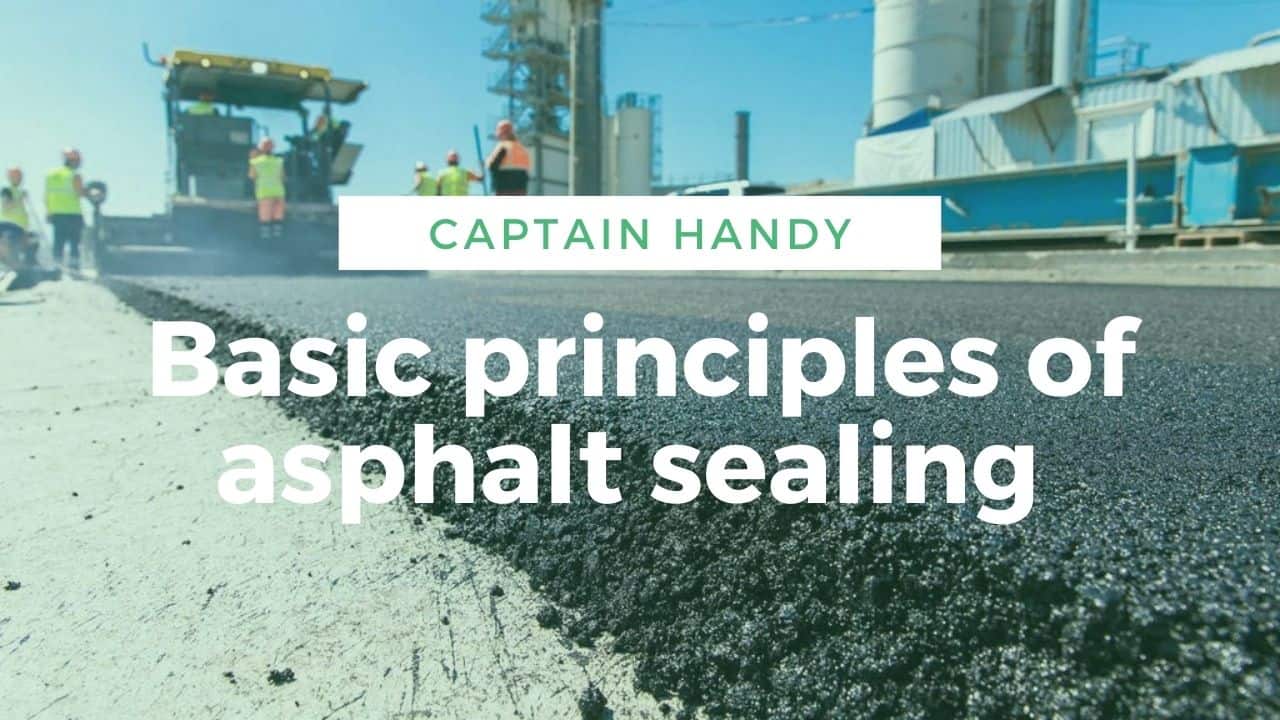
Table of Contents
Sealing principles
Asphalt sealing of pavement takes place in layers. If the technology is followed, asphalt sealing consists of several layers:
- the bottom layer;
- binder layer;
- wear layer.
For the wear layer (surface layer) classic asphalt concrete, crushed-mastic asphalt concrete, and porous asphalt concrete are used.
The asphalt concrete should be asphalt sealing to a degree that increases the density or decreases the porosity of the asphalt layer. The number of air cavities should be reduced to the recommended values to achieve the required degree of compaction.
As a result, the stability of the layer is improved and thus its resistance to deformation is increased. The durability of the surface layer also depends on the degree of asphalt sealing.
Together with the asphalt sealing work, there must be simultaneous leveling to ensure ride comfort, so the wear layer must have a continuous and smooth surface, but provide maximum traction of the wheels with the road.
Influence of mixture composition on compaction
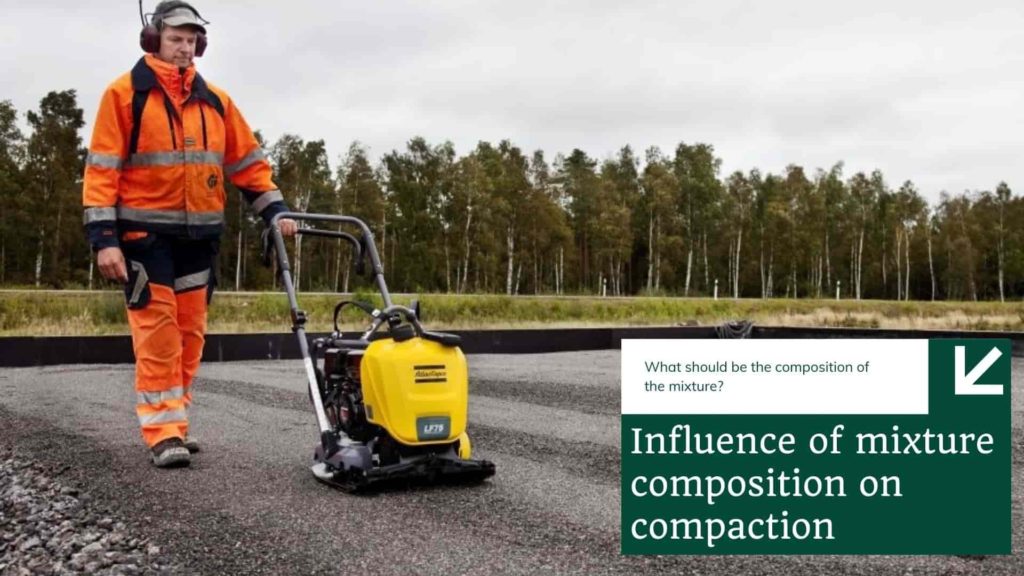
Asphalt mixture can be different in composition depending on the purpose (it is necessary to consider the nature of the load on the roadway) and climatic conditions. That is why the formulation of asphalt mixtures varies and with it the asphalt sealing properties. The properties are primarily influenced by the composition and size of the mineral components included in its composition. Another important component on which the viscosity depends is the bitumen and its temperature.
For heavily-used roads, mixtures with high resistance to deformation under load are used. As a rule, such mixtures include large-sized minerals, i.e. they contain a large number of stones of large fractions, crushed stones in crushed sand, and thick bituminous mortar. Such mixtures are very difficult to compact and require a great deal of effort and heavy machinery.
When paving low-intensity roads, mixtures with less stone content and significantly more sand are used, as well as soft bituminous mortar. Such mixes are easily compacted, but due to their characteristics they can easily be deformed during laying, so they require special control and time for curing. If the process cycle is violated, the material itself may shift or waves may form on the roadway.
Asphalt Sealing. Influence of mixture temperature on compaction
The effort required to lay asphalt is affected by the temperature of the mixture. As a rule, asphalt sealing begins when the temperature drops to 140-100 degrees and is finished when the mixture cools down to 100-80 degrees. These temperature requirements are due to the properties of the bitumen in the mixes: the lower the temperature of the bitumen, the greater its viscosity, and the more force the roller will need for asphalt sealing work. At higher temperatures, bitumen acts as a lubricant and reduces friction between the rollers and the mineral inclusions.
Asphalt sealing methods
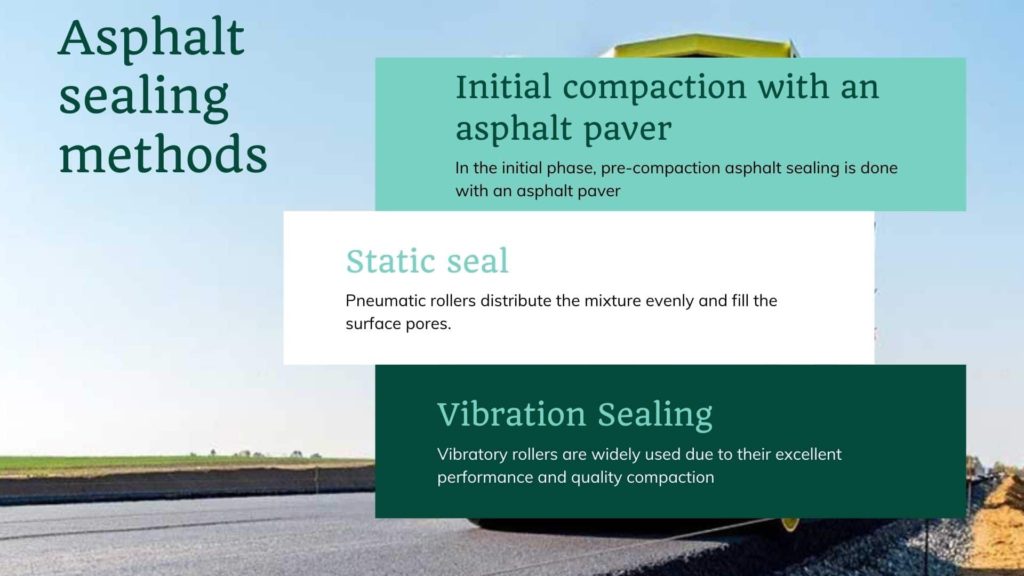
Initial compaction with an asphalt paver
In the initial phase, pre-compaction asphalt sealing is done with an asphalt paver. Precompaction with this type of equipment has an excellent effect on the initial layer and its characteristics, and also contributes to a better subsequent rolling, as long as the temperature of the mixture is high enough. This technology allows rolling to be done in less time, due to fewer passes by the roller.
If you start rolling without pre-compaction, you can disturb the evenness of the pavement, if the roller is too heavy, and even cause displacement of the material. If, however, compacting is carried out, it is recommended not to use the vibration mode during the first two runs of the tandem rollers.
Static seal
Due to the roller’s own mass, asphalt is statically compacted; for this purpose, both tandem and pneumatic rollers are used, but they give rather a poor compaction compared to vibrating rollers. Tandem rollers compact due to the linear load (kg/cm) of the drum, and pneumatic rollers due to the load from the wheels (t) and the air pressure in the wheels (MPa).
The use of these two types is advisable only after pre-compacting with an asphalt paver, or if it is necessary to lay a thin layer (wear layer) or asphalt with high porosity.
Pneumatic rollers have proven themselves for pre-profiling and compaction of soft mixtures or for asphalt sealing of road surfaces with low traffic volume. Pneumatic rollers distribute the mixture evenly and fill the surface pores.
Vibration Sealing
Vibratory rollers are widely used due to their excellent performance and quality compaction. They require fewer passes, thereby significantly saving time. Vibration from the roller reduces the friction of the material inside the mixture, and due to the weight of the roller and the dynamic load the density of the asphalt surface increases. Thus, for a vibratory roller, the key indicators are weight and vibration indicators: frequency and amplitude.
If the pavement of several layers is to be compacted, then heavy tandem vibratory rollers are used, which are capable of producing different amplitudes and frequencies of vibration of the rollers.
The operating speed for such rollers ranges from 3 to 6 km/h.
However, vibratory rollers should be used with caution, as a large number of passes can lead to loosening of the material and disturb the structure of the pavement due to excessive vibration.
Equipment for asphalt sealing
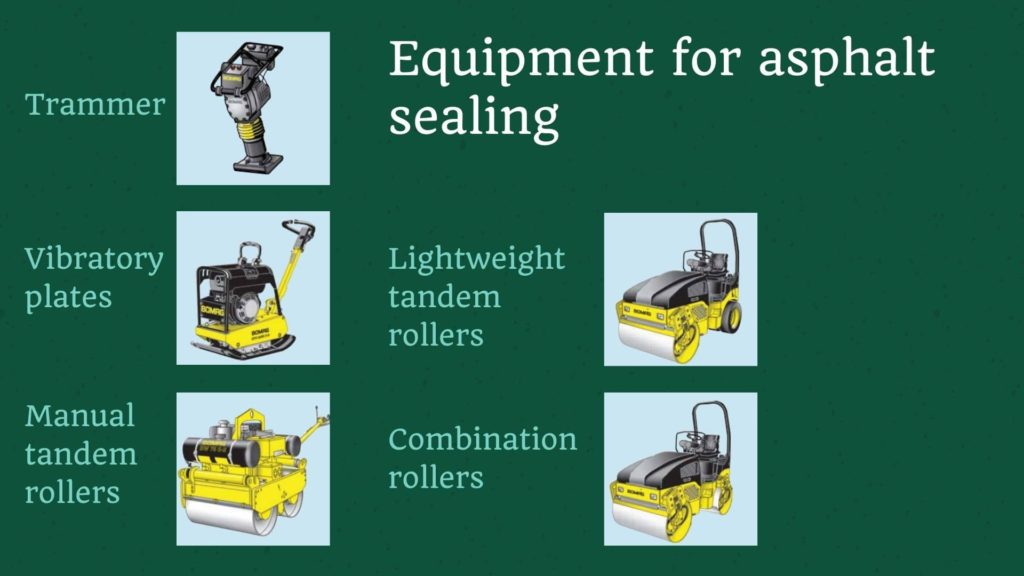
Manual equipment for asphalt compaction
Trammer
Vibratory rammers (rammers) refer to the means of small-scale mechanization. Their main area of application is limited spaces inside buildings, in areas adjacent to walls, fences, communication elements (e.g. manholes), etc. The weight of such rammers usually does not exceed 60-80 kg and are equipped with 4-stroke gasoline or, less often, diesel engines. The crank drive transmits a rapid vertical reciprocating motion to the ramming shoe.
Vibratory plates
Vibratory plates also belong to small-scale mechanization and are used for compacting small areas in confined spaces, they can be straight-running and reversible, their weight varies between 50 and 150 kg, and their working width is between 45 and 60 cm. They are equipped with gasoline or diesel engines. The directional vibrator is driven by a V-belt and a centrifugal clutch. The movement is controlled by adjusting the direction of action of the vibrator.
Manual tandem rollers
The weight of the accompanying rollers is 600-1000 kg, and the working width is from 60 cm to 75 cm. The drive of the rollers is either mechanical – with a two-stage gearbox, or hydrostatic, they work with double vibration.
Lightweight tandem rollers
The lightweight tandem rollers with articulated frames are available from 1.3 to 4.2 t in weight and working widths from 80 cm to 138 cm. Both rollers are hydrostatically driven and have a vibratory system.
Combination rollers
Combi rollers are based on a vibrating roller and a set of wheels. They are great for compaction of asphalt on sloped surfaces, as well as for repair work and rolling of footpaths and parking lots. The combination rollers are available in weight from 1.5t to 2.5t, and 7t to 10t.
Steering systems
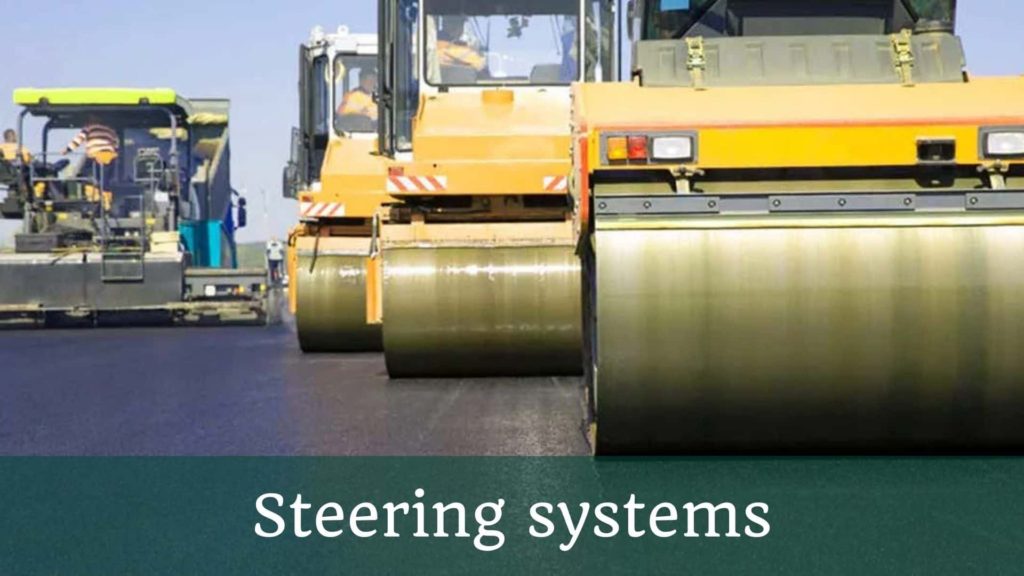
On rollers with controlled drums, they can turn simultaneously (synchronized operation) or each individually (front or rear), and also allow crabbing (with drum offset of up to 120 mm). These rollers are optimally suited for work on small sites (intersections, traffic circles, sharp turns) as well as for work on large construction sites (highways and freeways).
With rollers with steerable drums, the possibility of “crabbing” is an advantage. The “crabbing” allows the weight of the roller to be distributed over a large area, while the roller itself is not too deep. With this method, the initial compaction of sensitive materials with high asphalt temperature is greatly simplified, and “ironing” of large areas is possible, and the center of gravity of the roller is shifted away from the unstable edge of the asphalt surface.
In tandem rollers with the articulated frames, the drums are connected to each other by a central pivot.
The design allows the drums to move on the same path even when making turns. In “crabbing” mode, the rear roller is offset to the left or right in relation to the front roller. Due to the design, the rollers can be offset in relation to each other.
The benefits of using the “crabbing stroke” are obvious: it’s also possible to work near curbs or close to walls of buildings or fences, rational work with the edge compaction cone, as well as the ability to avoid the formation of traces from the roller with sharp edges on the surface of the asphalt.