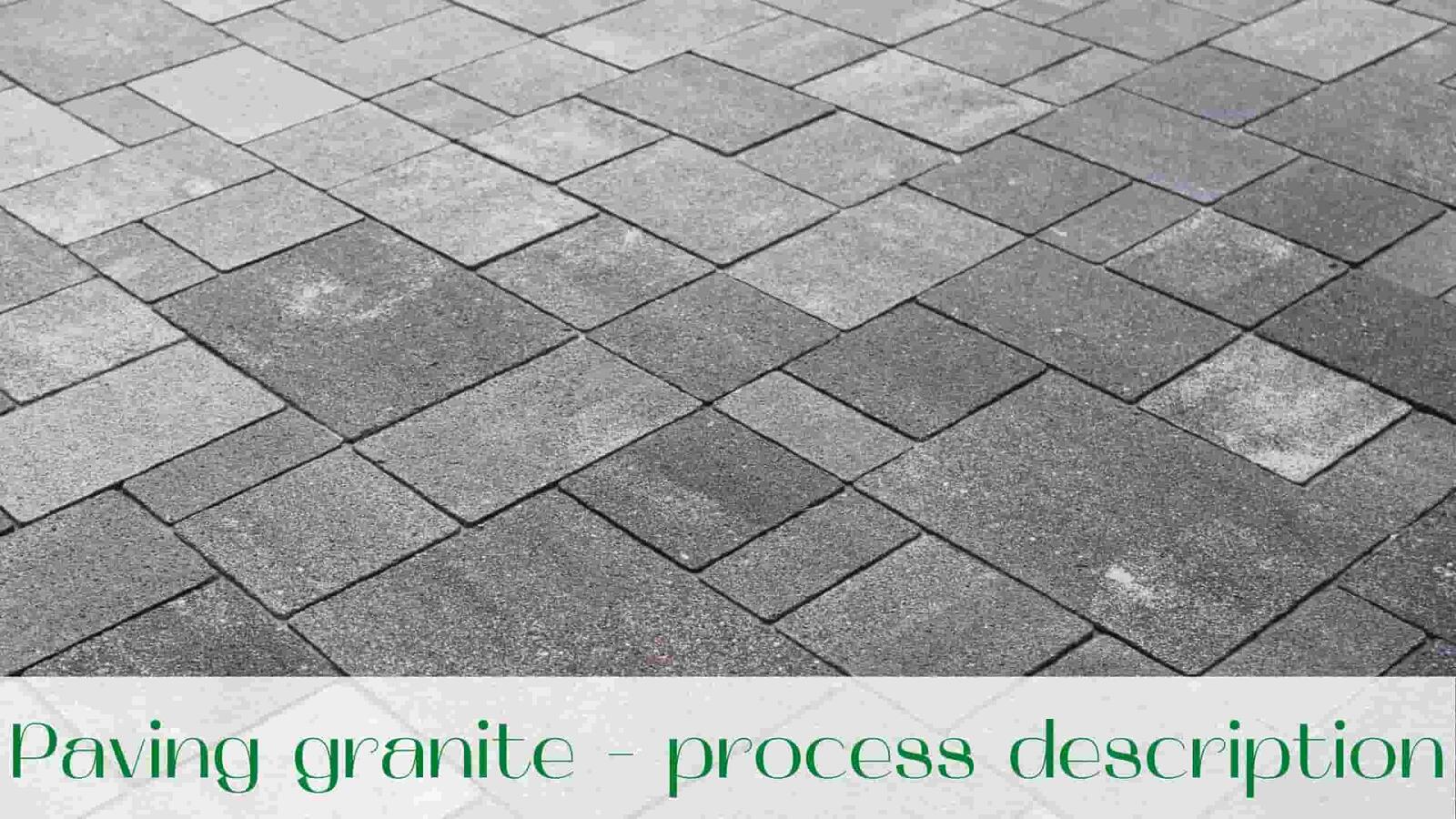
If you have bought a granite paving stone and want to independently make paving of the chosen site, in this article the information on technology of paving granite will be collected.
Table of Contents
1. Markings of a site for the subsequent paving by a paving granite stone
It is necessary to define the boundaries of the section, find out what objects will interfere (protrusions, bends, pipes, etc.). Further it is necessary to investigate a ground on which paving granite stone will be laid. To check up a ground on its uniformity if the ground is not uniform β to take measures on its consolidation go replacement of a part of a ground on more dense.
At designing of boards it is necessary to consider a slope of water, reference corners, points of installation of beacons.
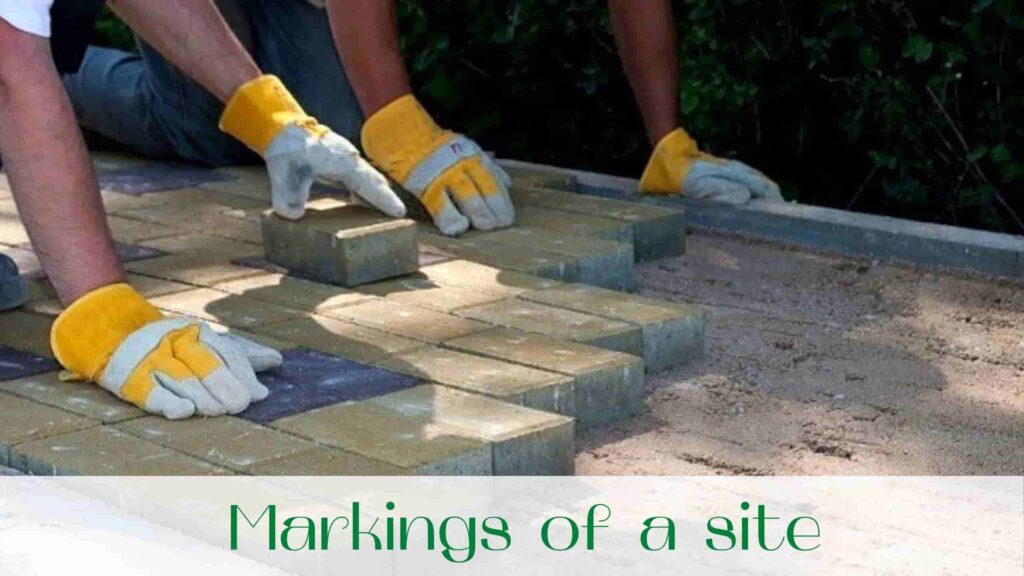
2. Preparing the ground for paving
The quality of granite paving is always a carefully prepared foundation. If the foundation work is not done correctly β your granite stone, the paving stone will not last long. In a few years you will already see subsidence marks, flooded areas, cracked stonesβ¦
The first procedure in preparation of the base is removal of the top layer of soil, in its place layers of crushed stone and sand. Then fix these layers with dry mix. Each layer needs to be tampered with β manually or with equipment that can be rented.
Subsequent paving of paving stone is only possible after all layers have been evenly distributed and compacted.
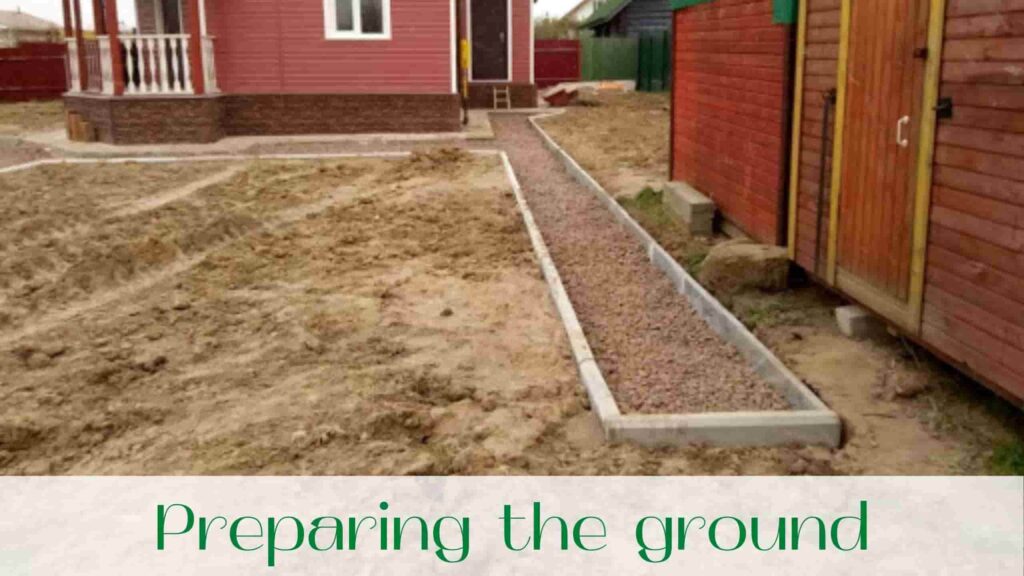
3. Paving tracks with paving granite stones (paving slabs) on a concrete base
Here, the technology is simpler than working with unprepared soil. Almost here, we have a paving stone base ready for laying. It is used in areas where the pavement will be subjected to high loads. To begin with, a paving court is excavated, which is the same area as the paving area.
The depth is usually chosen within 30-40 cm. The area is evenly filled with 10-15 cm of crushed stone. Then the tramway is manually driven by a vibrating machine.
Then the formwork is made and fastened into which the concrete will be poured and fixed before it cures. After the concrete has dried up, we distribute a layer of dry mixture 3-5 cm thick across the concrete. Here we have the paving site ready for you.
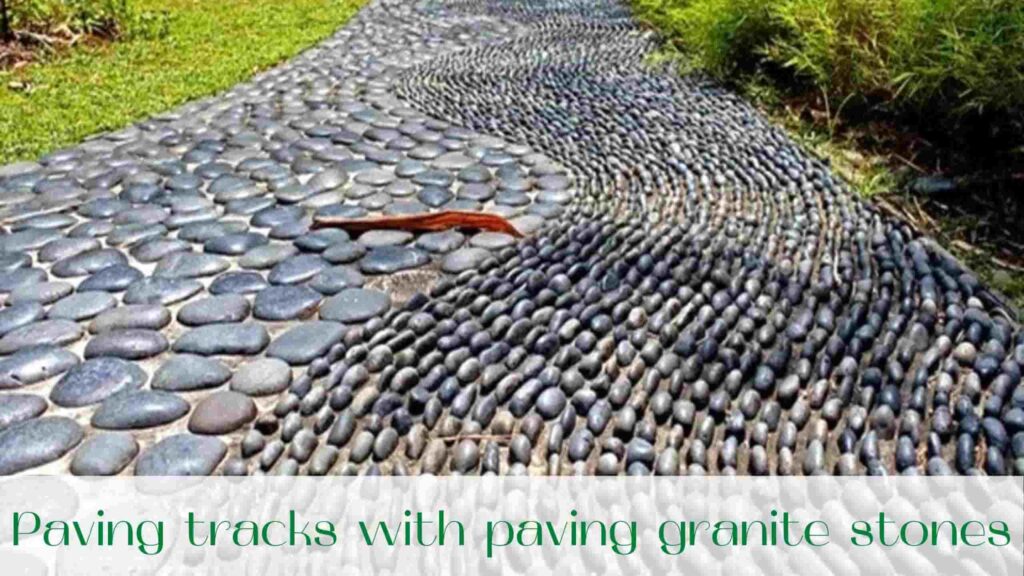
4. Power of a paving granite stone on a dry mix
One more common method of laying paving granite stone is paving on dry mix. It is necessary to dig out the area of paving to a depth of 30 cm. Then it is filled with a layer of crushed stone in 10-15 cm and tamped with the available method.
Then the crushed stone is covered with a layer of 10 cm of sand and also tamped. When tamping sand can be used to water it β this allows the sand to more effectively fill the space in the crushed stone. Then the dry mixture of 4-6 cm is filled in. Such a foundation becomes the basis for the entire paving technology of the paving stone to become a much better .
5. Paving granite paving stone on the sand
Granite stone paving is often used for garden paths, paths in kindergartens, hospitals. This method is used where there will be no high load on the paving stone. For this purpose, the soil is removed from the selected area, at a depth of 20-25 cm.
A geotcan (flat water-permeable polymeric (synthetic or natural) textiles, nonwoven, woven or knitted, used in geotechnics or other building applications in contact with the ground and/or other building materials) is placed at the bottom of the excavated area to prevent the various plants from breaking through the cracks between the stone. Crushed stone is poured onto the surface of the fabric in a layer of approximately 10 cm. The crushed stone must be compacted in a quality manner.
Then a 10 cm layer of sand is poured in and compacted. As a result we have a ready platform for packing of a granite paving stone.
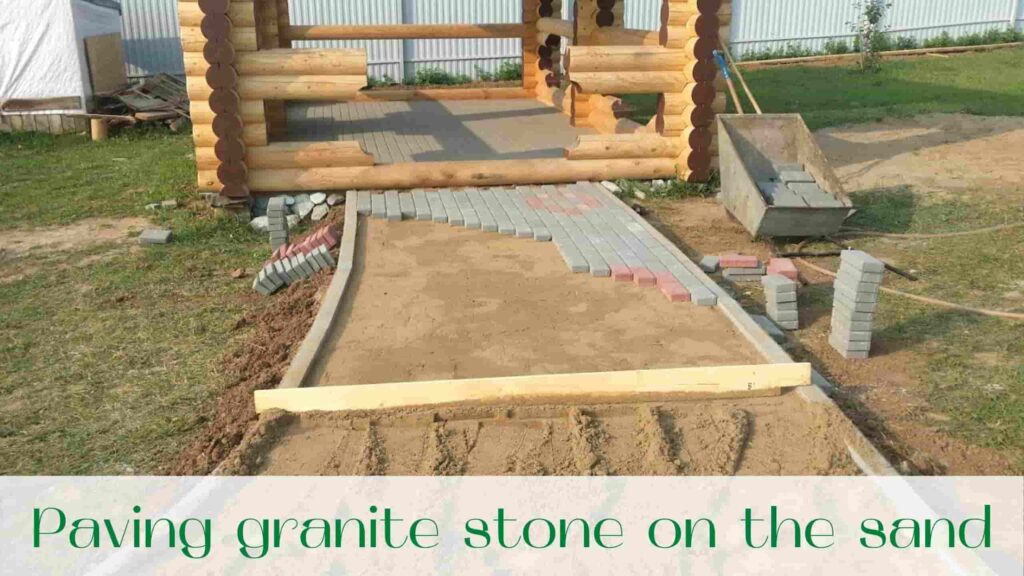
6. Setting up a curbstone
The final stage is the fixation of the curbstone. It is necessary that the territory where the granite paving stone was laid was fixed and did not allow to crawl or squeeze under the influence of the external ground. First of all it is necessary to dig out a trench which will pass along a path or already marked area. This trench must match the depth of the kerb installation.
Then we prepare a concrete mortar. The kerb stone should be installed in the concrete mix at half its height, the stones should be placed at the level, they should be installed and fixed with the concrete mortar that has not yet frozen. The kerb is fixed immediately after the concrete has hardened and this is only done on the outside of the paving operation.
If the preparation of the base and the kerb stone laying are not of good quality, what are the consequences?
Poor quality laying, over time, will cause the formation of puddles, deformation of the laid stone, irregularities, elevations or failures, reducing the life of granite products. If all is made correctly β water does not remain on a tile, after all everything is made under a small slope. There should not be any backlashes (differently plants or water will seep through slots) and even the knocked down drawing, absence of symmetry too concern poor quality packing.